Global industry projects to hit $1.3b in sales by 2027
A global protein shortage poses challenges for ensuring high-quality food production. To address this, the animal food industry has relied heavily on the importation of protein-rich materials, but there are limitations: soybean meal, for example, comes with environmental and social issues tied to deforestation in the Amazon, and fishmeal supplies are sourced from finite global fish stocks. Given the growing global population and food security issues, the animal nutrition industry is actively seeking more sustainable and locally sourced protein options.
Insects are increasingly being recognized as an innovative and viable solution, with the global insect protein market estimated at $343 million in 2021 and expected to grow to $1.3 billion by 2027.
After years of research and development, insect meal is now seen as a prospective new feed ingredient that is en route to widespread industry adoption. And an array of black soldier fly larvae meal products designed specifically for aquaculture have recently hit the market.
A ‘stable’ solution
The use of black soldier fly (Hermetia illucens, BSF) larvae is an especially promising frontier, proven to produce high-quality proteins while using minimal arable land and having a negligible impact on the environment while upcycling food waste.
This week, BioMar and Agronutris announced a long-term partnership to develop the next generation of BSF meals designed for the needs of aquaculture. The product, called Ultra’in, is a protein-rich solution for animal nutrition that’s made of dehydrated and defatted black soldier fly larvae. The insect meal has a highly qualitative nutritional profile that can meet animal nutrition needs – its high rate of proteins and comprehensive essential amino acid profile makes it a viable alternative to fishmeal in aquaculture.
“Black soldier fly meal has always been an interesting prospect that could be well suited for aquafeeds,” said Fernando Norambuena, global category manager, novel raw materials, at BioMar. “Agronutris has developed a scalable model for black soldier fly to be able to meet the nutritional and sustainability profile required by us and the industry.”
The BSF has a short development cycle, requiring only four weeks to grow from egg to adult. With optimized rearing conditions and expertise in insect nutrition, the larvae reared at Agronutris can multiply their weight 10,000-fold within only two weeks. Once they are mature, the larvae are collected and transformed into valuable ingredients for animal feed.
Fly guys: Canada opens the door for insect-based feed companies
Through detailed attention to its feedstock sourcing, 12 years of research and development achievements and significant industrial investment, BioMar says that “the Agronutris solution” will bring “a stable, high-quality product” with a high sustainability performance demonstrated by a robust life-cycle assessment.
“For insect meal to successfully make its way into aquafeeds, it must demonstrate high nutritional value and support good growth and health for the fish and shrimp,” said Chris Haacke, director of business development at Agronutris. “Our innovative product has a great nutritional profile that is well suited for the aquaculture industry. At Agronutris, we are working closely with BioMar to create the ideal product that will meet their ambitious sustainability parameters.”
Overall, Agronutris’ mission to supply low environmental impact feed alternatives aligns with BioMar’s ambitious sustainability plan that aims to source 50 percent of ingredients from a circular and restorative economy and lower its feed carbon footprint by one-third by 2030.
“A truly sustainable insect meal should be decoupled from the human food supply chain and fed off a substrate based on waste foods and byproducts,” said Vidar Gundersen, global sustainability director at BioMar. “With Agronutris, we see a viable, scalable model for producing black soldier fly meal that could see this product become a good source of nutrition in aquaculture.”
A truly sustainable insect meal should be decoupled from the human food supply chain and fed off a substrate based on waste foods and byproducts.
‘An exciting opportunity’
Insect meal is also trending on the other side of the world. Nutrition Technologies, a biotech company headquartered in Singapore and operating in Malaysia, recently signed an MoU agreement with Sumitomo Corporation – a leading Fortune 500 global trading and business investment company with 131 locations in 66 countries and regions. Founded in 2015 by two British entrepreneurs, Nutrition Technologies manufactures sustainable animal feed ingredients and biofertilizers, using a unique combination of biotechnology and BSF larvae to recycle nutrients from agricultural and food processing by-products.
To grow their insects, the company combines beneficial microbes and BSF larvae using a low-energy, zero-waste production model, rearing the larvae on clean and traceable agro-industrial byproducts. As a tropical species, the BSF larvae grow quickly and efficiently in the Malaysian climate – meaning that very little energy is required to grow or breed the flies. The company currently ships industrial volumes of material throughout Europe, Asia and South America, from the two-hectare factory in Malaysia.
This latest MoU, which is valued at $100 million, will allow Sumitomo to distribute Nutrition Technologies products into the Japanese market for use in a range of sectors, including pet food and aquafeed products.
“This distribution agreement not only secures supply for our existing customers and the strength of demand we have for future production, but emphasizes our commitment to the success of Nutrition Technologies, and underlines the strategic alignment between the two companies,” said Masahito Uno, general manager of the Life Sciences Division of Sumitomo Corporation.
In 2021, Nutrition Technologies scaled up to industrial production with the launch of its two-hectare factory in Johor, Malaysia, with plans to build several similarly sized facilities across Southeast Asia in the next five years. According to the company, it’s now one step closer to developing a sustainable circular economy within the agricultural sector.
“This is an exciting opportunity for Nutrition Technologies to extend its commercial reach in Japan, thanks to Sumitomo Corporation’s extensive distribution network and aligned companies within their group,” Nutritional Technologies stated in a press release. “This extensive market network and in-depth consumer insight will facilitate the Japanese market to access sustainably manufactured insect-based products, creating a more sustainable and equitable food system in the process.”
World’s largest fly factory attracting investors eyeing aquafeed expansion
‘It won’t happen overnight’
The insect sector has seen investments totaling nearly $1 billion, but there are nonetheless challenges to widespread industry uptake. For starters, few companies are yet to reach industrial scale because of multiple technological hurdles, including the high costs. This reality has led some start-ups to pause and even pivot.
Recently, French insect-based ingredient maker Ÿnsect announced plans to “refocus its strategy” on high-margin markets (like pet food), shut a production plant and cut jobs after raising 160 million euros (U.S. $177 million) from investors.
In its latest round of fundraising in 2020, Ÿnsect brought in more than 315 million euros (U.S. $345 million), of which about 175 million euros (U.S. $192 million) was capital and the rest in debt and subsidies. The company also announced agreements in December to build insect ingredient production sites in the United States and Mexico, has signed sales deals for 180 million euros (U.S. $197.8 million) over three years and is reportedly in talks for an additional 1 billion euros (U.S. $1.09 billion), of which more than half is for pet food, according to Reuters.
But the technology remains expensive, making the insect meal pricier than plant-based alternatives. As such, the company will redirect the money to finance new projects and expand its flagship vertical insect farm in Amiens in northern France, which is the world’s largest active insect production site. At the facility, farmed insects, such as mealworms, are ground down to produce proteins for aquaculture, livestock, pet food, fertilizers and human nutrition.
“In an environment where there is inflation on energy and raw materials but also on the cost of capital and debt, we cannot afford to invest loads of resources in markets which are the least remunerative (animal feed), while you have other markets where there is a lot of demand, good returns and higher margins,” CEO and cofounder of Ÿnsect Antoine Hubert told Reuters, referring to pet food, human nutrition and fertilizers.
Despite challenges, insect ventures continue to pop up, enticed by the emerging insect market. In January, deep tech company Volare, which produces insect-based protein, plans to build its first industrial-scale insect factory in Järvenpää, Finland. When opened, the facility will produce about 5,000 tons of environmentally friendly protein and lipids annually. Volare’s circular protein is used in fish feed and pet foods among others.
“We produce high-quality protein and lipids from the side streams of food production, and this has an extremely positive impact on the environment,” said Tuure Parviainen, Volare’s CEO. “With the new facility, we will be able to respond to the growing demand for climate-friendly protein in Europe.”
Volare has applied its insect-based protein to dog food and bird food, but the products are also suitable for instance feed applications for fish and other animals. The industrial-scale facility will be the first of its kind in Finland and one of the few to operate in Europe. As the facility uses Volare’s own unique technology, the protein production process will consume almost 30 percent less energy compared to similar solutions.
“It is true that our eating habits are becoming more and more sustainable slowly – but this won’t happen overnight,” said Parviainen. “However, we can change the dietary habits of fish and pets much faster and make a direct impact on the emissions.”
Follow the Advocate on Twitter @GSA_Advocate
Now that you've reached the end of the article ...
… please consider supporting GSA’s mission to advance responsible seafood practices through education, advocacy and third-party assurances. The Advocate aims to document the evolution of responsible seafood practices and share the expansive knowledge of our vast network of contributors.
By becoming a Global Seafood Alliance member, you’re ensuring that all of the pre-competitive work we do through member benefits, resources and events can continue. Individual membership costs just $50 a year.
Not a GSA member? Join us.
Author
-
Lisa Jackson
Associate Editor Lisa Jackson is a writer who lives on the lands of the Anishinaabe and Haudenosaunee nations in Dish with One Spoon territory and covers a range of food and environmental issues. Her work has been featured in Al Jazeera News, The Globe & Mail and The Toronto Star.
Tagged With
Related Posts
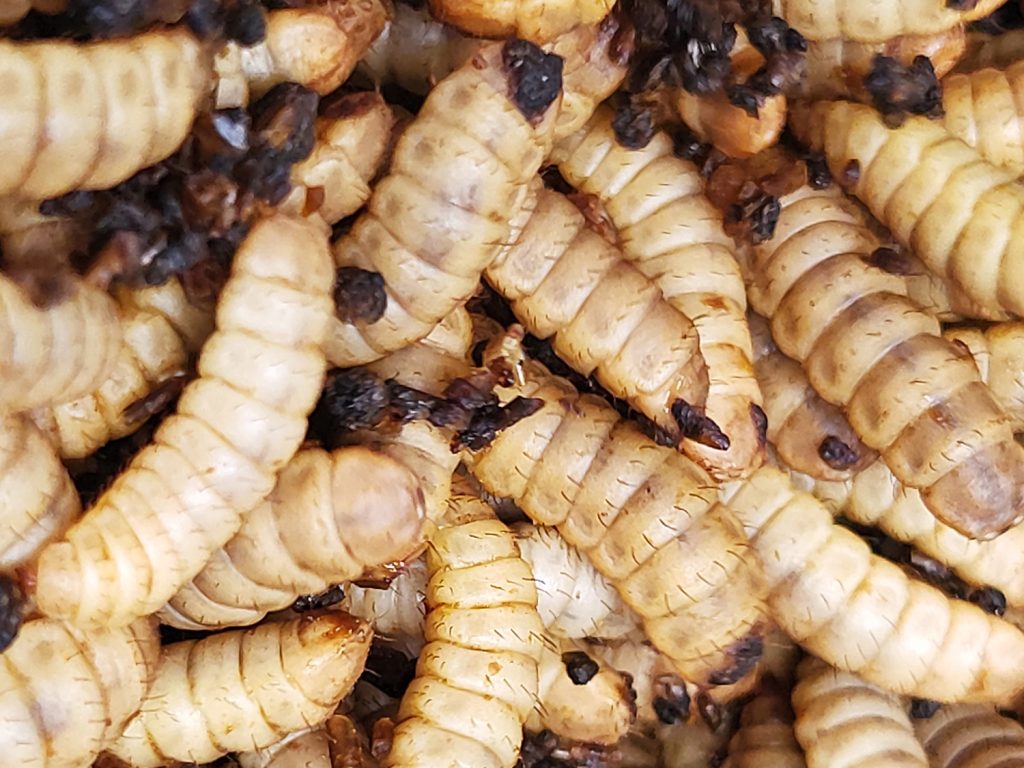
Aquafeeds
Bioactivity of black soldier fly larvae meal
Black soldier fly larvae meal has anti-inflammatory molecules that may alleviate inflammation but is outperformed by quercetin in this capacity.
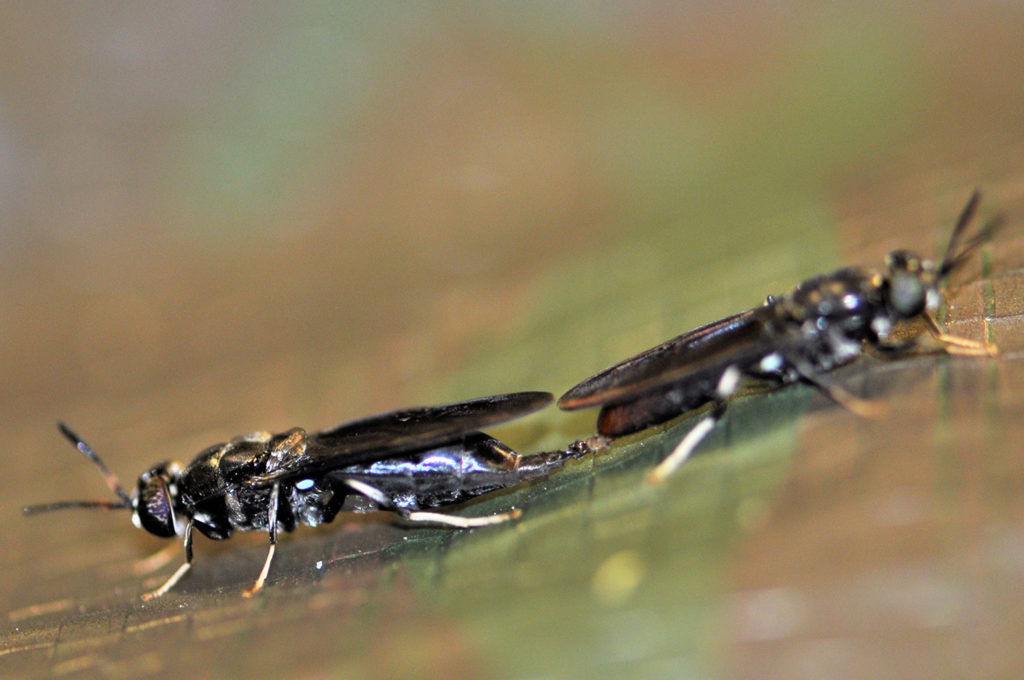
Aquafeeds
Black soldier fly larval production in a stacked production system
Study describes development and evaluation of an “all-in-one” stacked system for indoor production of black soldier fly larvae.
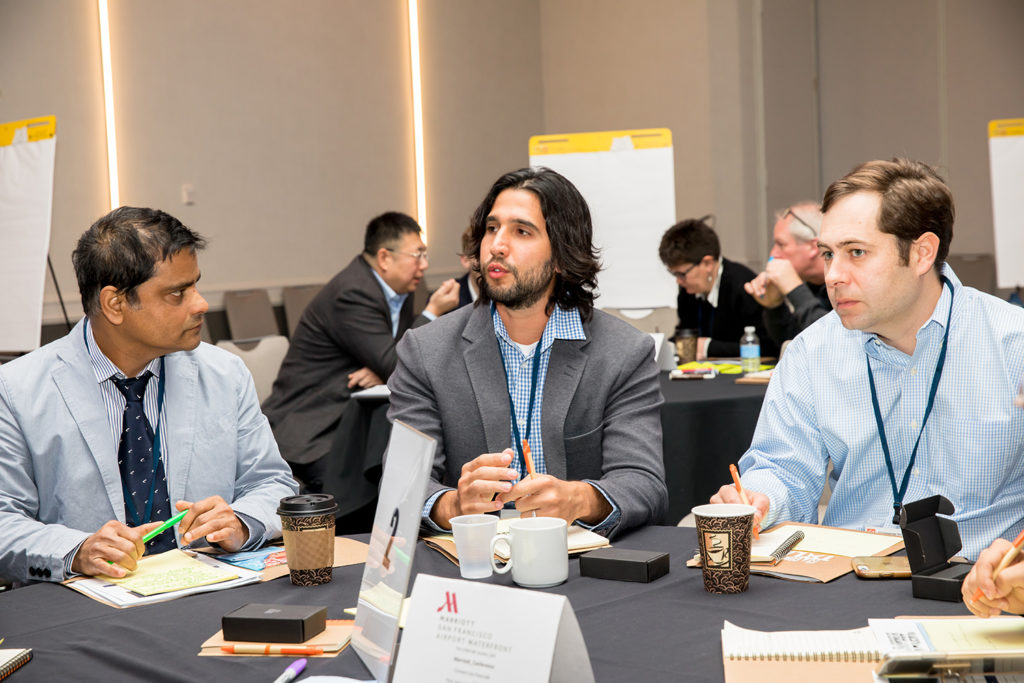
Aquafeeds
Aquafeed moonshots at the F3 ‘talent show’
At the F3 (fish-free feed) Companies Got Talent event in Burlingame, Calif., last week, alternative (non-marine) aquafeed ingredient companies spoke of decoupling aquaculture from fishmeal and fish oil in their quest for greater sustainability.
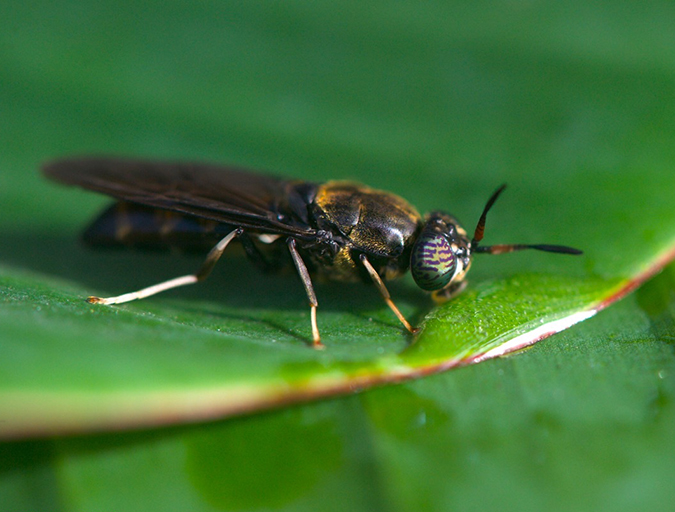
Aquafeeds
Buggin’ out: Tapping the potential of insect meal in aquaculture
Black soldier flies are gaining interest as a leading alternative ingredient in aquafeeds. But will the “ick” factor be a turn-off? Advocate contributor Clare Leschin-Hoar investigates.