Norwegian firm AKVA Group ‘showcasing the circular economy’ by making aquaculture pens from recycled plastic
Aquaculture equipment specialist AKVA group is on a circular economy mission. Two years after using recycled plastic to produce walkways for marine net pens, it is collaborating with Plasto and Oceanize to build the world’s first aquaculture pens made entirely from recycled materials.
Load-bearing structures in aquaculture pens mainly consist of virgin plastic because of material-quality requirements set by a technical standard (NS 9415, 2009). But AKVA group aims to challenge this standard by proving that recycled plastic from used pens can meet the same quality requirements.
“Net pens have been recycled in Norway for decades, but this has primarily been synonymous with heat recycling in which the pens are granulated and the granulate burned in a special power plant,” Arnstein Hosaas, innovation director at AKVA group told the Advocate. “Net pens are made from polyethylene (PE), a hydrocarbon that keeps its quality remarkably well. Over the years, we realized that we could use the granulate from discarded net pens to make new ones. After successfully producing walkways, we thought why not make an entire pen?”
With support from Handelens Miljøfond, a Norwegian retailers’ fund, discarded plastic pens from Aldersundet in Lurøy are cut up and granulated by Oceanize before being shipped to Plasto and AKVA group to produce parts for new pens. Norway’s aquaculture generates up to 12,000 tons of plastic waste each year, so hopes are high that this latest work will spur the sector to make important choices toward a more responsible future.
“We can be a leading example by showcasing the circular economy and giving the public an intuitive understanding of how this happens,” said Hosaas. “There has been a lot of talk about the circular economy for many years, but my impression is that not many people can relate to what it means.”
Trials and initial feasibility studies show that net pens made from recycled materials have significant potential and are very slow to deteriorate. Quality is also consistent, while the main components from old pens can be reassembled in a new and more modern configuration.
“The ability to re-utilize old pens to make completely new ones is a first,” said Hosaas. “The main benefit from this project is the very local, regional circular economy concept. We think that it can be an important way of showing that the aquaculture industry has a leading role toward a more sustainable way of producing quality food.”
Extensive quality control measures and quality assurances are needed before recycled plastic is used, while manufacturers must control the quality of recycled plastic before it can be incorporated into net pens. There are also other challenges. Having overcome industry regulations, the next step is to match the quality and quantity of material from old pens with market expectations, and all machinery must be used in an optimal way so that production is commercially sound and meets the high demand for quality and accuracy.
Hosaas said that Norway’s aquaculture is leading the way in many areas when it comes to recycling. The most common materials used in the sector such as nylon for nets, plastic for pens and steel for feed barges are all generally recycled, but the task now is to make their reuse more effective.
For example, nylon can be recycled into new products, but it can deteriorate quickly so it’s not normally re-used in aquaculture. Burning decommissioned equipment avoids local pollution and allows for energy production, but does not address the requirement for new material. Aquaculture is very eager to improve its environmental footprint, said Hosaas, and must now find a way to provide commercially sound products that are also better for the environment.
Going forward, AKVA group is due to construct and test its first prototype before offering it to clients as part of its product portfolio when technical integrity has been assured. Although there have been some questions about the reliability of a pen that is made from recycled materials, feedback has been positive. Hosaas believes that the product will be well-received in the market and shed light on the importance of recycling.
“The next generation of aquaculture products needs to be better by producing lower emissions, and be better quality without any negative price impact,” he said. “This can be achieved if minimizing a product’s environmental footprint becomes paramount for all new innovations. The key to successful recycling is to make it profitable. Norwegian aquaculture uses space along the coast and is very visible, so it’s expected to keep high standards. We want to show that just making everything new, from virgin material, is not necessarily the most effective way forward. It’s undoubtedly the most simple, but with our product, we will show that the circular economy is more effective than the use-and-discard economy.”
Follow the Advocate on Twitter @GSA_Advocate
Now that you've reached the end of the article ...
… please consider supporting GSA’s mission to advance responsible seafood practices through education, advocacy and third-party assurances. The Advocate aims to document the evolution of responsible seafood practices and share the expansive knowledge of our vast network of contributors.
By becoming a Global Seafood Alliance member, you’re ensuring that all of the pre-competitive work we do through member benefits, resources and events can continue. Individual membership costs just $50 a year.
Not a GSA member? Join us.
Author
-
Bonnie Waycott
Correspondent Bonnie Waycott became interested in marine life after learning to snorkel on the Sea of Japan coast near her mother’s hometown. She specializes in aquaculture and fisheries with a particular focus on Japan, and has a keen interest in Tohoku’s aquaculture recovery following the 2011 Great East Japan Earthquake and Tsunami.
Related Posts
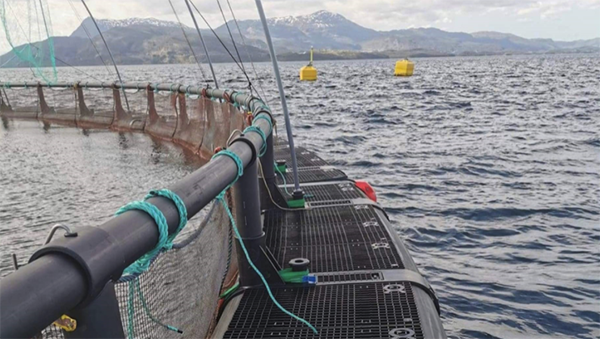
Innovation & Investment
AKVA develops ocean net pens without polystyrene
Aquaculture equipment manufacturer AKVA Group says its new ocean net pens are free of polystyrene, a plastic foam common in consumer packaging.
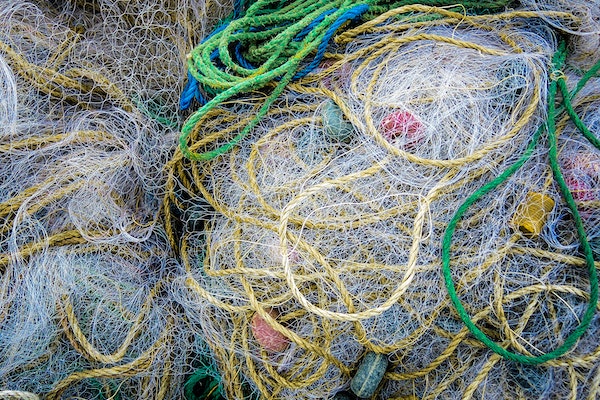
Responsibility
Can marine plastic from fisheries and aquaculture be upcycled into new things?
A SINTEF project is investigating how marine plastic used in fisheries and aquaculture can be turned into new products.
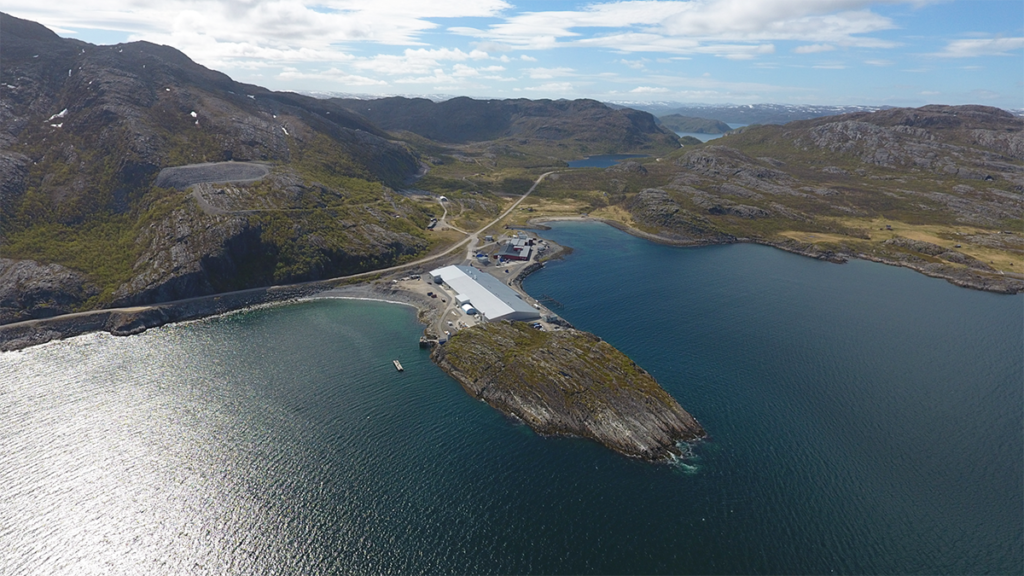
Responsibility
Sludge report: Finding value in Norway’s aquaculture waste
Bioretur converts aquaculture waste, or sludge, into fertilizer as demand for “circular economy” technologies grows.
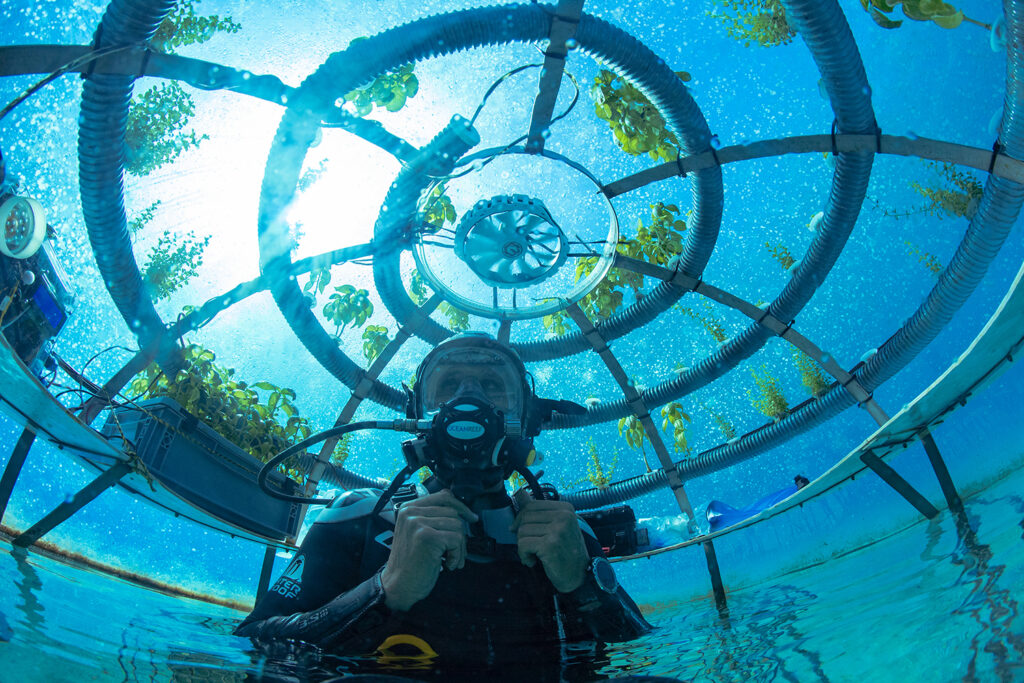
Innovation & Investment
20,000 lettuces under the sea: Could underwater agriculture be the future of farming?
Preliminary research suggests that emerging mariculture methods could provide alternatives to land-based agriculture and within recirculating systems.