Alternative to traditional U.S. ponds

The application of traditional pond-based shrimp-farming practices has met with limited success in the United States due to economic and environmental constraints. Among them, the water exchange required potentially increases the discharge of nutrient-rich water into natural ecosystems as well as the possibility of introducing harmful and pathogenic organisms.
In addition, seasonally low temperatures in the continental U.S. limit pond production systems to only one growth cycle per year. In conjunction with typically low productivity below 4,000 per hectare (ha), this short production period and high production costs limit competitiveness.
As an alternative, U.S. scientists have developed biosecure recirculating aquaculture systems. These systems consist of greenhouse-enclosed raceways for intensive to superintensive shrimp production with zero to limited water exchanges that can be operated year round.
When shrimp are reared at high densities without water exchange in recirculating units, the biofloc that develops in the culture water has several advantages for shrimp culture. These include increased recycling of wastes, allowing for an overall reduction in pollutant discharge to receiving bodies when waters are released at harvest. A lower amount of feed is required, which improves feed-conversion rates. Water quality is also more stable, and competition within the diverse microbial community apparently reduces pathogenic microorganisms such as vibrios.
Research at Waddell Mariculture Center
The Waddell Mariculture Center in Bluffton, South Carolina, USA, has been one of the pioneer institutions in the development of this type of system. During the last decade, its research on shrimp focused on an evaluation of the commercial feasibility of superintensive raceway production systems. These systems are operated without water exchange and with the addition of supplemental oxygen.
Stocking rates have been increased from 300 to 814 shrimp per square meter with yields of up to 69,000 kg per ha. Although some technical challenges remain to be resolved, research in pilot- and commercial-size raceways has demonstrated feasibility.
2007 growout experiment

Waddell Mariculture Center’s most recent experiment was conducted in a 271-square-meter super-intensive raceway production system. Two weeks prior to shrimp stocking, the raceway was filled with a mix of filtered ultraviolet-treated seawater and well water, creating a salinity of 20 grams per liter About 22.5 kg of alfalfa pellets were added to stimulate the development of a microbial community.
Juvenile Pacific white shrimp, Litopenaeus vannamei, of 1.68 ± 0.2 grams weight were stocked in mid-July at 581 shrimp per square meter. Ten-day old shrimp postlarvae had been purchased at a hatchery located in the U.S. Florida Keys and maintained in two 50-square-meter greenhouse-enclosed raceways for 63 days during the nursery stage.
Shrimp were fed a 35 percent-crude protein shrimp growout diet designed for superintensive systems. Feed supply was adjusted weekly based on an expected growth rate of 1.1 grams per week and a feed-conversion rate (FCR) of 1.6. Population was estimated assuming a mortality of 1 percent/week.
The amount of feed consumed in four feed trays, average weekly growth and estimated FCR provided valuable information to adjust feed supply. Feed was provided by hand broadcasting around the raceway four times per day during the first 92 days. Thereafter, only 25 percent of the feed was provided by hand during the first feeding, and the rest was delivered by automatic belt feeders over a 12-hour period.
Several water quality parameters were monitored (Table 1). To reduce the levels of nitrite nitrogen during the period in which nitrifier communities were becoming established, the heterotrophic bacterial community was stimulated by adding dextrose days 7 to 15 to increase the carbon:nitrogen ratio. Dextrose was added again for one week after day 106, when an unexplained decline in shrimp growth and slight increases in ammonia and nitrite levels were observed.
Venero, Average water quality parameters registered during a 146-day experiment, Table 1
Parameter | Mean | Maximum | Minimum |
---|---|---|---|
Temperature (° C) | |||
Morning | 28.2 ± 1.3 | – | 25.6 |
Evening | 29.1 ± 1.4 | 32.0 | – |
Dissolved oxygen (mg/l) | |||
Morning | 6.5 ± 1.2 | 9.1 | – |
Evening | 6.2 ± 1.3 | – | 3.5 |
pH | 7.1 ± 0.3 | 7.8 | 6.5 |
Salinity (g/l) | 18.6 ± 0.5 | 20.1 | 17.6 |
Alkalinity (mg/l as calcium carbonate) | 111.7 | 200.0 | 60.0 |
Total ammonia nitrogen (mg/l) | 0.2 | 0.7 | 0 |
Nitrite nitrogen (mg/l) | 0.800 | 3.400 | 0.009 |
Nitrate nitrogen (mg/l) | 144.8 | 299.8 | 1.8 |
Total suspended solids (mg/l) | 590.5 | 1,270.0 | 200.0 |
Volatile suspended solids (mg/l) | 307 | 460 | 55 |
Chlorophyll (ug/l) | 433.2 | 883.7 | 121.0 |
The clarifier unit started operating after day 28 at a flow rate of 6.48 liters per minute. The clarifier was too small for the raceway, however, so it did not reduce levels of total suspended solids (TSS) and volatile suspended solids (VSS). TSS remained 200-1,270 ppm, and VSS values were 55-460 ppm until the end of the cycle. At its most efficient flow rate, turnover time for the entire raceway was 21 days. Approximately 48 cubic meters of freshwater was added to compensate for evaporation.
On day 146, 1,877 kg of shrimp averaging 20 grams were harvested. The average growth rate was 0.88 grams per week (Table 2), and the FCR was 2.5. Average growth rate was 1.00 grams per week until day 99. It declined to 0.82 grams per week week for the rest of the cycle after shrimp reached 14-gram average weight. The reason for this decline is unknown.
Venero, Comparison of research and commercial-size superintensive greenhouse, Table 2
Oceanic Institute | Texas Agrilife Research Facilities | Waddell Mariculture Center 2003 | Waddell Mariculture Center Dec. 2007 |
|
---|---|---|---|---|
Raceway size (m2) | 337.0 | 68.5 | 271.0 | 271.0 |
Average depth (m) | 1.60 | 0.58 | 0.72 | 0.72 |
Weight at stocking (g) | 0.50 | 1.25 | 1.00 | 1.61 |
Stocking density (shrimp/m2) | 828 | 310 | 310 | 581 |
Final weight (g) | 18.3 | 16.6 | 16.6 | 20.0 |
Growout period (days) | 84 | 76 | 76 | 146 |
Growth rate (g/week) | 1.50 | 1.44 | 1.44 | 0.88 |
Yield (kg/m2) | 10.30 | 4.69 | 4.69 | 6.92 |
Yield (kg/ha) | 103,000 | 54,200 | 46,900 | 69,200 |
Survival (%) | 67.9 | 88.3 | 91.0 | 60.2 |
Feed-conversion ratio | 1.60 | 1.21 | 1.54 | 2.50 |
Total water use (l/kg shrimp) | 402 | 155 | 157 | 130 |
Water exchange (%/cycle) | 176.4 | 0 | 0 | 0 |
Evaluation
Waddell Mariculture Center researchers managed a commercial-size superintensive, zero-water-exchange raceway to produce a commercial fresh shrimp harvest during the cold months of the year in the United States (Table 2). A zero-water-exchange production record of 69,200 kg per ha was achieved while using only 60 l of 35 ppt saltwater to produce 1 kg of shrimp. This volume of water could be reduced still further if the same salt water is stored and used to refill another raceway for a new production cycle.
This type of water reuse can enhance the development of nitrifier communities in the system as well as significantly reduce economic and environmental costs for systems sited far inland.
Even though these production values are encouraging, the relatively low growth rate and high FCR reduce the profitability of this enterprise, especially if the product is sold at the market price of imported frozen shrimp. Previous research at the Waddell Mariculture Center in the same raceway at a lower stocking density of 310 shrimp per square meter produced better growth of 1.44 grams per week and an improved 1.54 FCR, but with lower productivity (Table 2).
Oceanic Institute
The Oceanic Institute in Hawaii, USA, obtained production records of 103,000 kg per ha with an average growth rate of 1.5 grams per week and FCR of 1.6. However, the facility exchanged about 14.7 percent water per week and estimated a total use of 402 liters water per kg shrimp produced.
Texas Agrilife Research
The Texas Agrilife Research facilities in Flour Bluff, Texas, USA, used smaller 68.5-square-meter raceways equipped with settling tanks and a stocking density of 310 shrimp per square meter to obtain harvests of 50,400-54,200 kg per ha. Production was slightly lower (46,000-50,000 kg/ha) when foam fractionators were used instead of settling tanks. The raceways operated with zero water exchange, reporting the use of 142 and 155 liters water per kg shrimp produced.
Perspectives
The relatively low growth rate and high FCR reported in the 2007 Waddell Mariculture Center study when the stocking density was increased to 531 shrimp per square meter indicated technical and production limitations remain to be addressed. The ammonia nitrogen and nitrite nitrogen peaks that occurred shortly after stocking may have been the most important factors responsible for reduced growth and survival. In addition to direct stress during the critical developmental growth stage, they might have caused some initial mortality that led to overfeeding and associated water quality deterioration.
As the Texas Agrilife Research Facilities studies demonstrated, the use of settling tanks may be critical to maintaining optimal growing conditions in these biofloc systems. Although a clarifier was used to remove solids produced in the WMC trial, its capacity was probably too limited to significantly improve water quality and associated shrimp growth.
Other aspects which may be considered as the system is scaled up for commercial applications include improving the designs of engineered systems that efficiently and cost effectively meet oxygen and supplemental heating demands. Further improvements could address the integration of automation, an emergency oxygen-backup system and better solids collection and waste treatment. Higher genetic quality of the shrimp stocks and the use of more-accurate methods to estimate the initial population could also improve the end results.
The results of these and other studies are revealing the tremendous biological potential of genetically improved specific pathogen-free stocks of L. vannamei. The key to translating these results into commercial competitiveness will be a focus on scale-up, maintaining consistency and improving efficiencies to reduce costs of production.
Currently, low shrimp market prices and high production costs limit superintensive production. However, in the short term, targeted direct sales to local consumers or upscale restaurants that demand “never frozen” shrimp can support higher prices for a quality domestic product.
(Editor’s Note: This article was originally published in the January/February 2009 print edition of the Global Aquaculture Advocate.)
Now that you've reached the end of the article ...
… please consider supporting GSA’s mission to advance responsible seafood practices through education, advocacy and third-party assurances. The Advocate aims to document the evolution of responsible seafood practices and share the expansive knowledge of our vast network of contributors.
By becoming a Global Seafood Alliance member, you’re ensuring that all of the pre-competitive work we do through member benefits, resources and events can continue. Individual membership costs just $50 a year.
Not a GSA member? Join us.
Authors
-
Jesus A. Venero, Ph.D.
Waddell Mariculture Center
South Carolina Department of Natural Resources
P. O. Box 809
Bluffton, South Carolina 29910 USA[109,111,99,46,108,105,97,109,116,111,104,64,50,56,115,117,115,101,106]
-
Brad McAbee
Waddell Mariculture Center
South Carolina Department of Natural Resources
P. O. Box 809
Bluffton, South Carolina 29910 USA -
Alisha Lawson
Waddell Mariculture Center
South Carolina Department of Natural Resources
P. O. Box 809
Bluffton, South Carolina 29910 USA -
Beth L. Lewis
Waddell Mariculture Center
South Carolina Department of Natural Resources
P. O. Box 809
Bluffton, South Carolina 29910 USA -
Alvin D. Stokes
Waddell Mariculture Center
South Carolina Department of Natural Resources
P. O. Box 809
Bluffton, South Carolina 29910 USA -
John W. Leffler, Ph.D.
Waddell Mariculture Center
South Carolina Department of Natural Resources
P. O. Box 809
Bluffton, South Carolina 29910 USA -
Craig L. Browdy, Ph.D.
Novus International
Charleston, South Carolina, USA
Tagged With
Related Posts
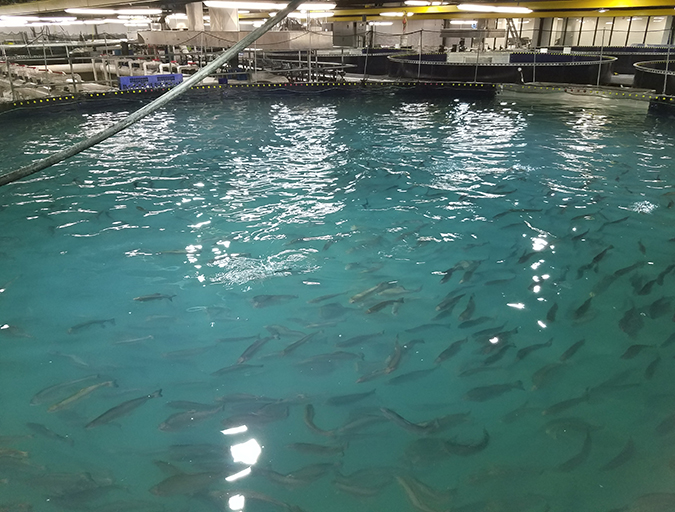
Intelligence
A land grab for salmon (and shrimp) in upstate New York
The operators of Hudson Valley Fish Farm see their inland locale as a pilot to prove that land-based fish farming, located in close proximity to major metropolitan markets, can be successful.
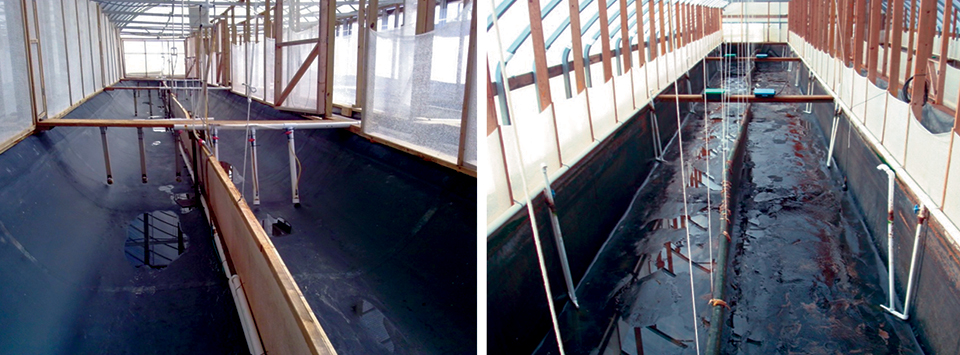
Responsibility
Advances in super-intensive, zero-exchange shrimp raceways
Research at the Texas AgriLife Research Mariculture Laboratory is investigating ways to improve the economic viability of super-intensive raceways for shrimp production.
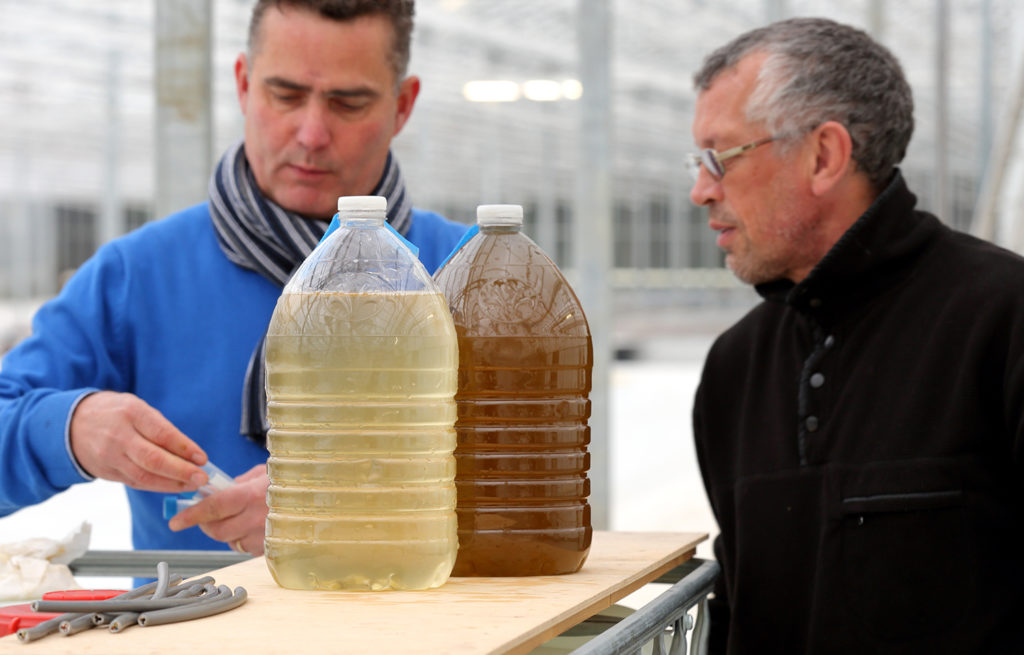
Innovation & Investment
Algae innovators aim to freeze out early-stage shrimp losses
A greenhouse in Belgium believes its innovative shrimp feed product, made from freeze-dried microalgae, packs the necessary nutrients for the crustacean’s most vulnerable life stage: the first three days of its life.
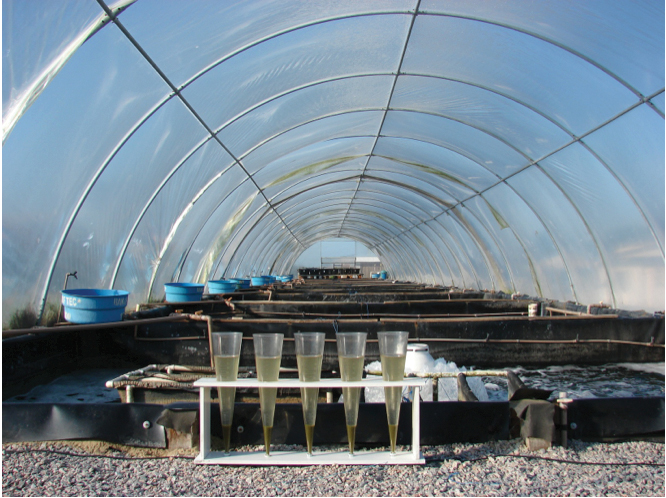
Health & Welfare
Ammonia addition enhances microbial flocs in nursery phase for Pacific white shrimp
In a study, “pre-fertilization” in the nursery phase of a biofloc system for shrimp was tested. The objective was to accelerate the biofloc formation to minimize ammonia concentrations, avoiding high peaks during culture.