Biological performance not lost with lower-protein diets in intensive floc conditions

The Pacific white shrimp (Litopenaeus vannamei) is the most widely farmed shrimp worldwide today. Much of this achievement can be accredited to its predominant omnivorous feeding habit, which can spare expensive nutrients in commercial feeds.
Protein ingredients make up the bulk of the formula costs in shrimp diets. Although feeds with less than 25 percent crude protein can be used at densities of 10 animals/m2 or less in growout, protein levels can rise as high as 40 percent under higher stocking densities.
Since microbial floc production systems are rapidly emerging in the commercial culture of L. vannamei, it becomes crucial to evaluate the role of high-protein diets under these conditions. Bioflocs, or microbial detritus, are rich in several essential nutrients that support and enhance the growth of L. vannamei under intensive culture.
Experimental design
The authors conducted a study to determine how reducing the protein content of a diet would affect the growth performance of L. vannamei reared in an experimental microbial floc culture system.
Thirty circular tanks of 1,000-L volume were used for the study. Each tank was covered with nets and equipped with four aeration stones 15 cm from the tank bottom. In addition, two floating PVC airlifts were placed in each tank for vertical water circulation.
Juvenile L. vannamei weighing 3.53 ± 0.77 grams each were stocked in rearing tanks at 50, 75 and 100 shrimp/m2. Five replicate tanks were assigned for each stocking density, totaling 15 tanks under microbial floc culture (MFC) and 15 under regular intensive culture (RIC).
Two diets were prepared. Diet RIC consisted of a commercial shrimp diet with 36.9 percent crude protein and 5.5 percent lipids that was ground, cooked and repelleted with lab manufacturing equipment. The MFC diet was formulated to contain less than 25 percent crude protein and a final carbon:nitrogen (C:N) ratio of 12:1. This lab-made diet was a combination of the RIC diet mixed with a low-fiber commercial poultry feed, dried molasses and a synthetic binder (Table 1).
Nunes, Ingredient composition and proximate analysis of experimental diet, Table 1
Ingredient | Content (g/kg) |
---|---|
Poultry feed1 | 540.3 |
Shrimp feed2 | 407.3 |
Molasses3 | 50.0 |
Synthetic binder | 2.4 |
Proximate Analysis | Content (g/kg |
Crude Protein | 235.2 |
Fat | 425.0 |
Fiber | 43.8 |
Ash | 98.8 |
Moisture | 79.9 |
1147.3 g/kg crude protein, 37.1 g/kg fat, 61.1 g/kg fiber, 65.3 g/kg ash
2368.9 g/kg, 55.0 g/kg fat, 28.0 g/kg fiber, 100.6 g/kg ash
353.4 g/kg, 0.4 g/kg fat, 1.8 g/kg fiber, 191.6 g/kg ash
Nunes, Performance of L. vannamei farmed at different densities, Table 2
Performance Variables | System | Shrimp Stocking Density 50 Shrimp/m2X | Shrimp Stocking Density 75 Shrimp/m2X | Shrimp Stocking Density 100 Shrimp/m2X | Shrimp Stocking Density P Value |
---|---|---|---|---|---|
Initial body weight (g) | RIC | 3.99 ± 0.35a | 3.28 ± 0.22b | 3.58 ± 0.14ab | < 0.05 |
Initial body weight (g) | MFC | 3.70 ± 0.36A | 3.26 ± 0.75B | 3.31 ± 0.25B | N.S. |
Final body weight (g) | RIC | 21.22 ± 1.10a | 18.57 ± 1.26b | 17.27 ± 1.29b | < 0.05 |
Final body weight (g) | MFC | 20.22 ± 0.43A | 17.99 ± 1.67B | 16.95 ± 0.35B | < 0.05 |
Weekly growth (g) | RIC | 1.68 ± 0.12a | 1.49 ± 0.11ab | 1.33 ± 0.12c | < 0.05 |
Weekly growth (g) | MFC | 1.61 ± 0.04A | 1.33 ± 0.05B | 1.48 ± 0.16B | < 0.05 |
Final survival (%) | RIC | 92.8 ± 7.6a | 72.7 ± 10.7ab | 67.2 ± 21.7b | < 0.05 |
Final survival (%) | MFC | 81.6 ± 15.6 | 85.1 ± 10.4 | 80.0 ± 15.7 | N.S. |
Final yield (g/m2) | RIC | 771 ± 116 | 751 ± 158 | 766 ± 308 | N.S. |
Final yield (g/m2) | MFC | 629 ± 167A | 883 ± 152AB | 1.002 ± 225B | < 0.05 |
differences among densities in each system (α = 0.05)
Shrimp were daily fed to satiation from feeding trays at 7 a.m. and 4 p.m. Animals under RIC received the commercial diet alone, whereas for MFC, dried molasses mixed with seawater was added once daily based on feed consumption and a targeted C:N ratio of 20:1 for the culture water.
Water preparation
Prior to shrimp stocking, clean seawater in each rearing tank was fertilized with sodium nitrate, sodium silicate and monoammonium phosphate. To boost phytoplankton growth, greenwater from six nursery tanks was collected, mixed and inoculated at 20 L/m3. Rearing water was aerated for three more days before the shrimp were stocked. At the start of the trial period, only tanks intended to operate under the production of microbial flocs were treated with a commercial microbial mixture.
No water exchange took place during culture in any of the tanks, but the tanks were filled whenever necessary with seawater lost due to evaporation. No other attempts to correct water quality were made during 76 days of culture, which included four days of acclimation. Biofloc formation was measured every three days from all tanks.
Results
Water salinity and temperature reached means of 36 ± 2.6 ppt and 31.6 ± 0.93 degrees-C, respectively. No significant variation was observed for these parameters between culture systems or among stocking densities used (P > 0.05). In both types of systems, water pH decreased from over 8 at the onset of the study to less than 7 close to harvest.
Within each system, pH also varied as a function of stocking density, particularly when culture water with 50 and 100 shrimp/m2 under regular intensive culture were compared (7.7 ± 0.51 and 7.4 ± 0.55, respectively). Daily oxygen measurements taken at 3 a.m., 4 p.m. and 11 p.m. never fell below 2.23 mg/L, with a mean value of 3.53 ± 0.77 mg/L.
Despite the reduction in feed protein content, shrimp had very similar performance under both microbial floc culture and regular intensive culture. Some parameters varied as a function of stocking density and/or culture system. Final shrimp survival did not differ between the MFC and RIC treatments, but only the MFC system was able to support 100 shrimp/m2 without a deleterious effect on survival (P > 0.05).
Shrimp survival in the RIC system decreased progressively as higher densities were adopted, whereas the MFC showed more consistent survival rates. This suggested that without water exchange, the RIC system was not able to support a high shrimp biomass, either due to insufficient dissolved-oxygen levels or a failure in recycling excess nutrients from feed remains and shrimp feces.
Shrimp weekly growth, final body weight and yield showed no differences between culture systems. Under both conditions, growth was acceptable and always above 1.3 grams/week, but there was a trend toward slower growth and lower body weights at harvest with increasing stocking density. This became more pronounced under the MFC system, particularly when 50 shrimp/m2 was compared with 75 and 100 shrimp/m2 (P < 0.05). Shrimp yield for RIC did not surpass the 0.8 kg/m2 threshold, whereas for the MFC, it reached as high as 1.0 kg/m2.

Microbial flocs
Microbial floc material was formed in both the RIC and MFC systems, although molasses was not added to the RIC tanks to control C:N rations in the water. Tanks with 75 and 100 shrimp/m2 under MFC increased the amounts of floc material in the water throughout the culture period. However, a biofloc plateau seemed to be reached at five to six weeks of culture in tanks with 50 shrimp/m2 and in all stocking densities operating under RIC conditions. Under MFC conditions with 75 and 100 shrimp/m2, biofloc production continued to increase until shrimp harvest.
Data collected in this study presented strong evidence that the biological performance of L. vannamei was not lost when lower-protein diets were used under intensive floc conditions. If these results can be replicated within a commercial culture setting, the method can give a significant competitive advantage to those operating or shifting to microbial floc systems.
(Editor’s Note: This article was originally published in the May/June 2010 print edition of the Global Aquaculture Advocate.)
Authors
-
Alberto J.P. Nunes, Ph.D.
Instituto de Ciências do Mar
Av. da Abolição, 3207 – Meireles
Fortaleza, Ceará 60165-081 Brazil[114,98,46,109,111,99,46,108,111,117,64,110,112,106,111,116,114,101,98,108,97]
-
Leandro Fonseca Castro, M.S.
Instituto de Ciências do Mar
Av. da Abolição, 3207 – Meireles
Fortaleza, Ceará 60165-081 Brazil -
Hassan Sabry-Neto, M.S.
Instituto de Ciências do Mar
Av. da Abolição, 3207 – Meireles
Fortaleza, Ceará 60165-081 Brazil
Tagged With
Related Posts
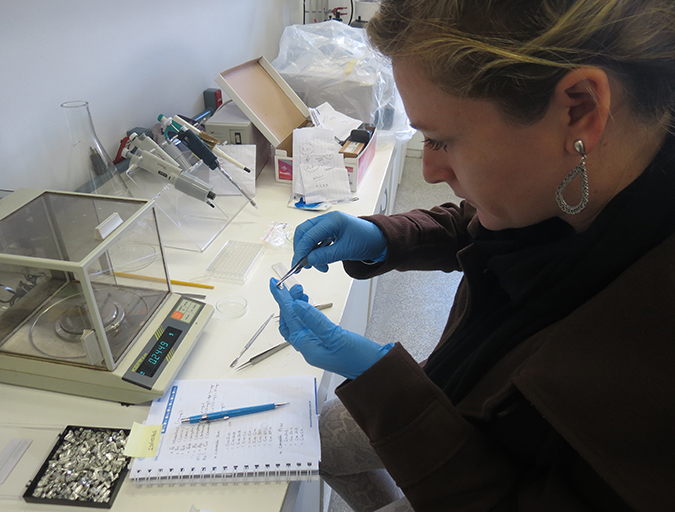
Aquafeeds
Biofloc consumption by Pacific white shrimp postlarvae
The stable isotopes technique with δ13C and δ15N can be used to determine the relevance of different food sources to shrimp feeding during the pre-nursery phase of Litopenaeus vannamei culture. During this trial, different types of commercial feed, microalgae, Artemia sp. nauplii and bioflocs were used as food sources.
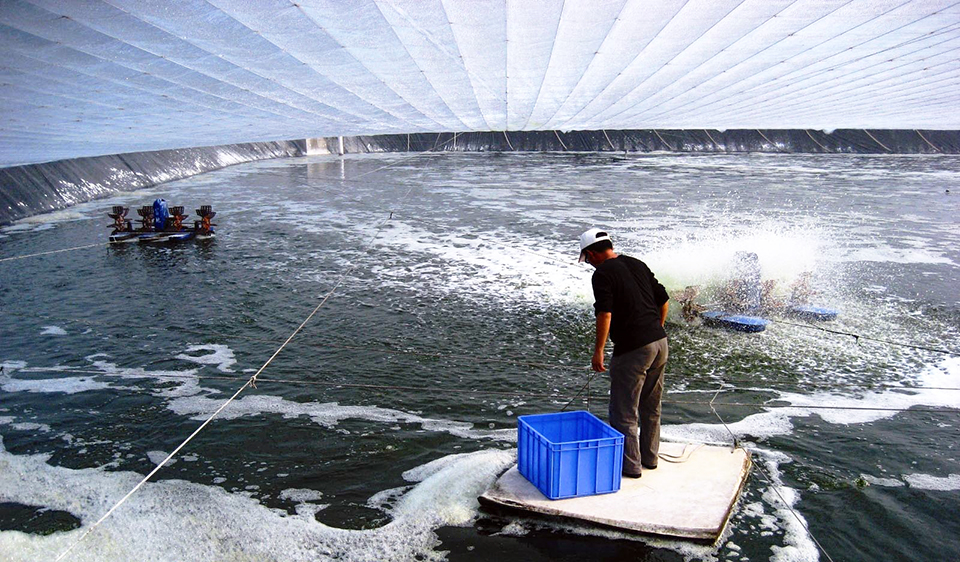
Health & Welfare
Biofloc technology expanding at white shrimp farms
Biofloc technology provides high productivity, low feed-conversion ratios and a stable culture environment. Also, with viral problems and rising costs for energy, biofloc technology can help deliver sustainable production at lower cost.
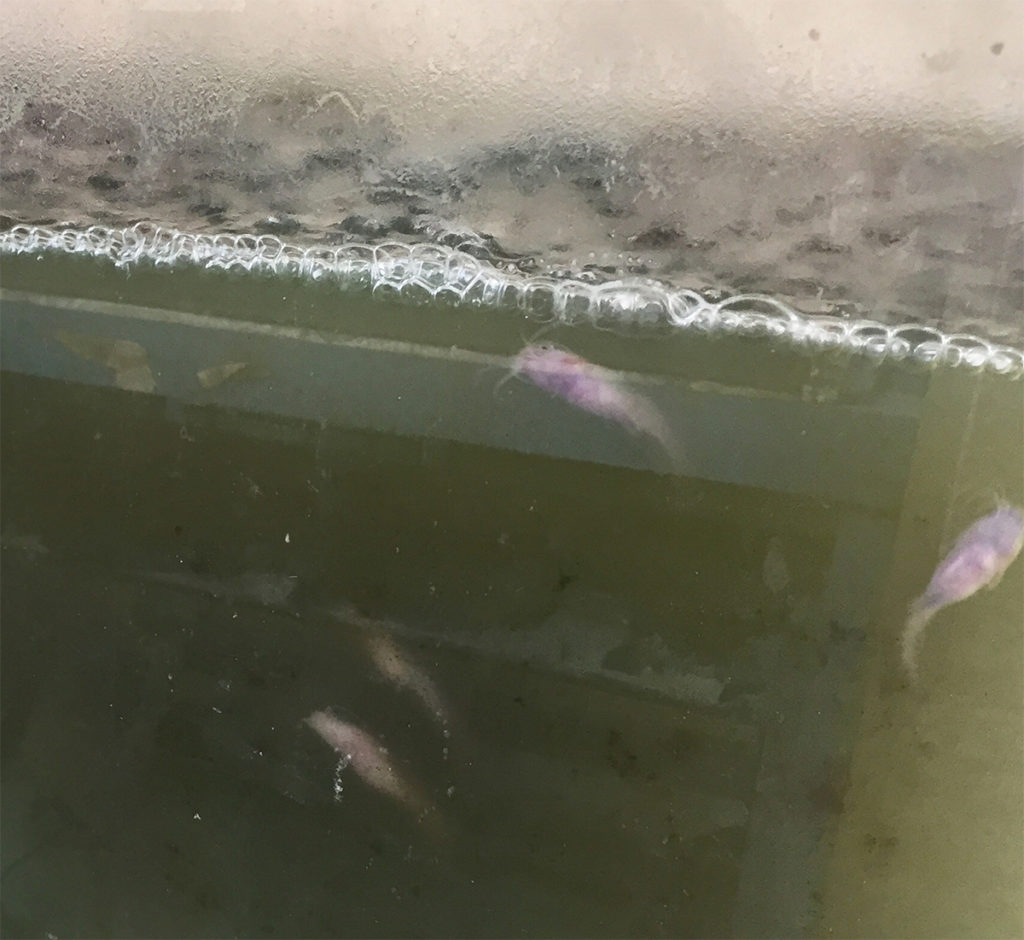
Health & Welfare
Biofloc technology holds potential for carnivorous fish species
Juvenile carnivorous African catfish performed well in biofloc-based systems, which could help produce better quality and more disease-resistant seed of this important aquaculture species and support the expansion of African catfish farming industry.
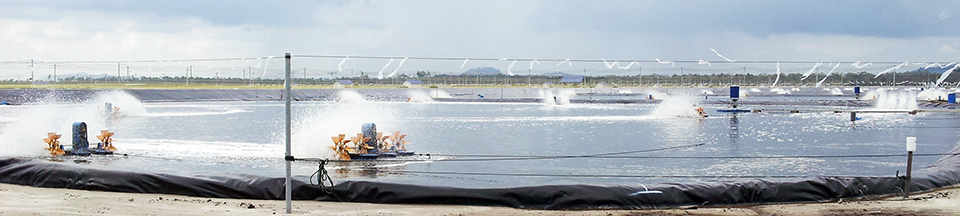
Health & Welfare
Biofloc technology: Possible prevention for shrimp diseases
Facing emerging viral problems and rising energy costs, the use of biofloc technology in biosecure systems offers an answer for sustainable shrimp aquaculture. The main attributes of biofloc systems in reducing disease risk include the fact that low water exchange improves pathogen exclusion.