Offshore aquaculture concepts range from submersible, rigid framed structures to flexible, floating structures that ride, rather than resist, waves
Introduction It is widely forecast that the world faces a future seafood deficit of many millions of tons. It is also generally accepted that the world’s marine capture fisheries have reached their maximum sustainable yield and, if the projected deficit is to be made up, the balance will have to come from aquaculture. Since global aquaculture production between 1984 and 1997 increased from 6.7 to 28.9 million metric tons, it is often assumed that aquaculture is well on its way to accomplishing this goal.
However, a problem with this assumption is that most of this increase was of low value, freshwater carp species. And, while these fish are vital to the diet of lowincome communities in many areas of the world where they are grown, carp are not favored by people with higher incomes, who prefer to eat other species, mostly of marine origin. Moreover, as income levels rise worldwide, demand for marine fish is increasing while the supply is, at best, static, and may be diminishing, as important stocks are over-fished. Can aquaculture make up for the deficit in these species? Since the oceans contain 97 percent of the earth’s water and cover two-thirds of its surface and, given what has already been achieved in freshwater aquaculture, it seems that this should be possible.
Emergence of farmed salmon
Of all the outstanding achievements in aquaculture in recent years, I think the one that points to the answer is the emergence of the farmed salmon industry. In an extraordinary period of development that has seen its production grow from nothing to over 800,000 tons in only twenty years, salmon farmers have shown what can be done, and hinted at what might be accomplished by learning to farm in the sea. In marked contrast to production from closed-system or pump-ashore farms, at-sea farming of salmon in cages has shown that this approach to aquaculture works on an industrial scale. In so doing, it has also shown that it could help, materially, to make up for a future shortage of marine fish, if space can be found along our coastlines where cage culture of fishes can be carried out.
Today, marine aquaculture takes place in confined areas along our coasts, where benign conditions make it possible for man to exert some control over the water he farms. Some farms are on shore; while others are in bays and inlets. But all of them compete for space with other users who value the same locations for other reasons, who often were there first and dislike newcomers. Almost everywhere, it seems the industry has to compete for the space it needs and is challenged by those who resent its presence. Yet, elsewhere along our coasts there is space in plenty, if we can learn to farm in the hostile waters of the open sea.
Offshore sea farming
The biggest challenge has been to develop fish containment systems that can function reliably in these “offshore” conditions, which is the term now most commonly used to describe this idea. This is not to say that farms have to be sited many miles out into open ocean. There are huge amounts of space along our coasts near to shore, but in order to use these, fish containment structures must be able to withstand storm events in open water when these occur.
There are almost as many inventors working on solutions to this challenge, at present, as there were early aviators at the turn of the last century trying to design the first airplanes; and just as many skeptics. Concepts range from submersible, rigid framed structures to flexible, floating support collars that ride, rather than resist, the waves. One approach, in particular, seems to have special potential and here I acknowledge a bias, because I have been involved for several years with the company that developed it. This is the idea of using floating spar buoys to provide stable, rigid support structures around which to build wave transparent and submersible cages. Having been model and field-tested over the last ten years, two designs are now used commercially and serve to illustrate the substantial progress that has been made.
Spar buoy cages

The Ocean Spar cage uses spar buoys as floating fence posts to hold the cage net in shape. The buoys are held in place laterally by anchor tension, while damping weights are hung below them to minimize vertical motion. This design creates a cage with little surface superstructure, which means that it is “transparent” to waves. In a storm, waves just pass through the cage rather than tossing it about. This greatly reduces fatigue and wear in cage components, and the resulting risk of failure. A net stretched over the top of the cage prevents fish from escaping as waves pass through (Fig. 1).
These cages have been used in locations with significant wave heights of up to seven meters and current speeds of up to 2.5 knots. They can be set up in series as squares, or rectangles, using common anchors, or as single cages with multiple sides and independent moorings, with no limit on ultimate volume.
An alternative design, Sea Station (Figs. 2, 3 and 4), uses a single spar buoy surrounded by a 25-meter diameter steel rim to form a frame. Rope spoke lines then create two cones that are enclosed by netting. Flooding or evacuating water from the spar buoy controls buoyancy. In this way the cage can be operated at the surface, where it offers only a limited profile to waves, or submerged, where it is completely protected from them.
In a recent test in Hawaii a Sea Station was held 12 meters below the surface for all of the seven months it took to grow 70,000 moi (Pacific threadfin) to market size. At the surface, Sea Station cages have performed so well in exposed sites that the designers still do not have a good sense of their wave height limit.
By design, the netting on both of these cages is held taut and moves little under the impact of ocean forces. This provides stable growing space for the fish and reduces wear and fatigue in the net, minimizing the risk of failure and maximizing service life. Moreover, the net itself is made from a new high tech fiber called “Dyneema,” claimed by its manufacturers to be the world’s strongest. This is then spun and woven into a web called “Ultra Cross,” in which the fibers pass straight through the intersections, rather than being knotted or knitted, as in the construction of other netting. This further limits wear and minimizes the loss of fiber strength that occurs in other net making processes.

The successful development of these and other open sea cages means that marine fish farming can now be started in parts of the world where this was not possible before, because the coastline provided insufficient shelter. Since this includes many tropical and sub-tropical countries, the prospect of farming a number of warm water marine fish is, therefore, greatly enhanced.
At the same time, expansion can now be contemplated in countries where farming already occurs, but where areas of available, sheltered water are limited. It would probably not be overstating the case to say that the advent of open sea cages has transformed the prospects for marine aquaculture worldwide. However, just because open sea farming is now possible, it does not mean it will happen. There are still other matters to consider.
Operations
To be economically viable on a large scale, a future offshore farming industry must develop fully integrated farming systems, where farm operations can be undertaken efficiently and safely in an environment that is often hostile to humans. The advent of reliable offshore cages is merely the first step, albeit a critical one. The next steps will build on lessons learned on farms in protected waters and adapt know how and equipment, as needed, from other marine industries. Key areas for further development include feed delivery, bio-fouling control, harvesting, and surveillance. Inevitably, the development process will be by trial and error, but at least it can now begin, and it is encouraging that experience to date suggests there are no major operational bottlenecks.
Costs

If they are to contribute significantly to our future seafood supply, offshore farms must be able to produce at a cost that meets the value expectations of the mass market. Salmon farmers understand what this means, having learned a painful lesson in the late ’80s as they started to produce larger quantities of salmon. They learned that high prices, based on small volumes produced early in the farming of a new species, can fall rapidly once up-market niches are full. When this happens, unless costs can be brought down, industry growth will stall. It is a lesson that those concerned with the development of all new aquaculture technologies would do well to heed.
The salmon farming industry responded to this challenge by greatly improving efficiency. In less than ten years, production costs in the world’s most efficient farms were halved, from about $5 per kilogram in 1990 to $2.20 to $2.50 per kilogram today.
As a result, the cost of the meat in a salmon fillet is now approximately the same as that of chicken breast meat. If this seems improbable, bear in mind that 60 percent of a salmon is fillet, whereas the yield of breast meat from a chicken is only 15 percent, with the remaining cuts having lesser value. Because of these efficiencies, markets for farmed salmon have continued to grow, and the industry now provides a good benchmark against which to measure the potential of other aquaculture processes.
Lessons that still have to be learned about operating offshore farms mean that initial operating costs are likely to be higher than for conventional cage farms. But as experience is gained, the ability to operate on a larger scale and in water of superior quality will reduce cost differentials, or even reverse them. Moreover, the benefits of larger scale will follow downstream, providing the opportunity for greater efficiency in processing, distribution, and marketing. The present high cost of performing these tasks is the reason why retail prices for salmon are still so much higher than they are for chicken breast, and represents a major opportunity for further cost reduction in the farmed salmon value chain.
Feeds

It seems likely that most of the candidate species for offshore farming will be carnivores. They are the species preferred by most consumers and those that are subject to the greatest pressure in our capture fisheries. But it is conventional wisdom to assume that growing carnivores is not sustainable, because they have to be fed on diets based on fishmeal. If a future is envisaged in which millions of tons of such fish will be farmed, will we be able to feed them?
Space does not permit a lengthy discussion of this question here, but the answer is almost certainly yes. Concerns about long-term supplies of fishmeal are real, albeit overstated by those opposed to aquaculture. But there are many other feed meals of both animal and vegetable origin that can, with suitable processing, be substituted for fishmeal in feeds for at least some species. Just because an animal is carnivorous in the wild does not mean that it is an obligate carnivore in captivity.
A more fundamental question is: might any of these fish be more efficient at converting these precious raw materials into edible meat than the pigs or chickens to which they would otherwise be fed? Should it be found that some fish are, in fact, more efficient than their terrestrial counterparts, when all factors are taken into account, it makes a compelling case for aquaculture, wherever it takes place.
Wastes
Evaluation of different forms of animal farming must also consider what happens to their metabolic wastes. In the open sea, these will be dispersed and naturally recycled in a huge volume of seawater. Again, it is conventional wisdom to assume that this is bad, that discharge of such wastes will have a so-called “negative impact.” But what about positive impacts? After all, fish wastes are a natural part of the marine ecosystem and higher concentrations of nutrients in some ocean environments are beneficial, as is the case in areas of marine upwelling. Moreover, natural assimilation in the ocean requires no inputs of man-made energy, in contrast to culture systems in which waste is treated internally.
On the other hand, wastes dispersed in the ocean can not be recovered in a conventional sense, though there are numerous observations to show that floating fish farms act as fish aggregation devices (FADs), and that species such as mullet benefit from the waste materials in the vicinity. The science and cost / benefit of all this seem to merit further research, or else invalid assumptions may lead to development of bad policy and ill-directed investment.
Regulations
The above discussion leads to the inevitable question of regulation. Installation of permanent structures in our open coastal waters clearly needs planning and direction and, most likely, the grant of private property rights. Different countries will handle this in different ways, depending on their social and economic priorities. For some it will be difficult, because the oceans are held in public trust and are perceived as nature’s last unconquered frontier. Putting fish farms in them is like fencing off the range. But if governments desire and/or expect that farmed fish will make up for shortages from our capture fisheries, there will be some difficult questions. And one of them is likely to be about putting fences in the ocean.
(Editor’s Note: This article was originally published in the February 2000 print edition of the Global Aquaculture Advocate.)
Now that you've reached the end of the article ...
… please consider supporting GSA’s mission to advance responsible seafood practices through education, advocacy and third-party assurances. The Advocate aims to document the evolution of responsible seafood practices and share the expansive knowledge of our vast network of contributors.
By becoming a Global Seafood Alliance member, you’re ensuring that all of the pre-competitive work we do through member benefits, resources and events can continue. Individual membership costs just $50 a year.
Not a GSA member? Join us.
Author
-
John Forster
Aquaculture Business Consultant
[109,111,99,46,110,101,112,121,108,111,64,114,101,116,115,114,111,102,106]
Tagged With
Related Posts
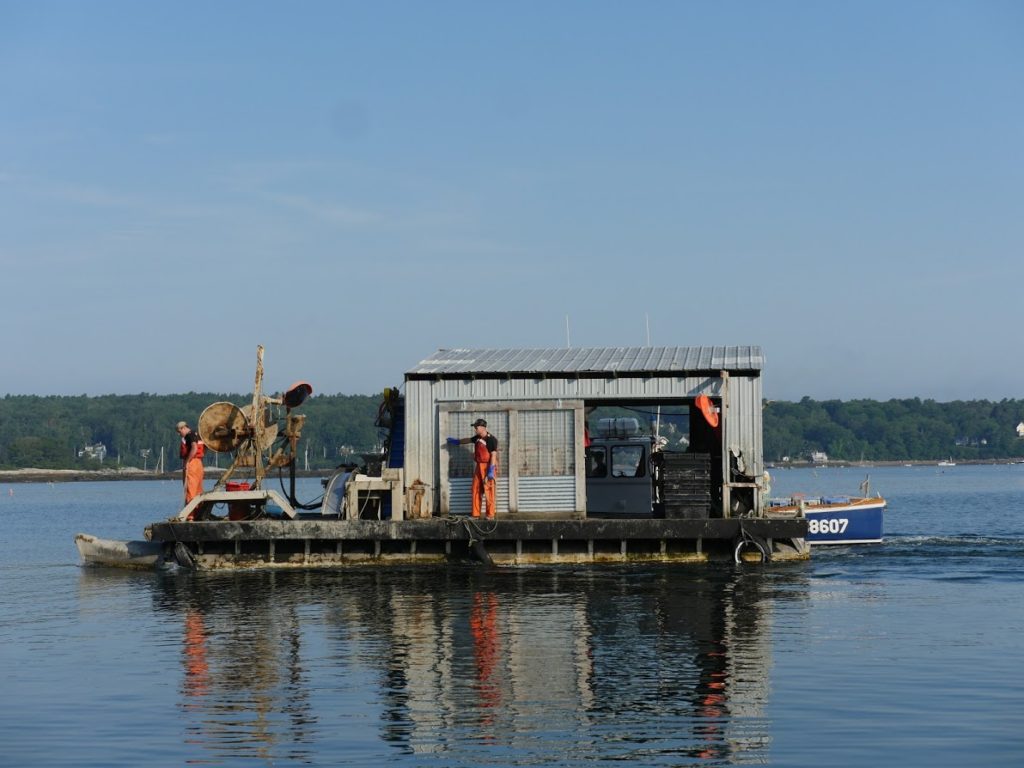
Intelligence
Can Americans’ perception of aquaculture change?
Perhaps the biggest barrier to aquaculture’s growth and development in the United States is public perception. There’s a lack of trust. And at the root of that is education.
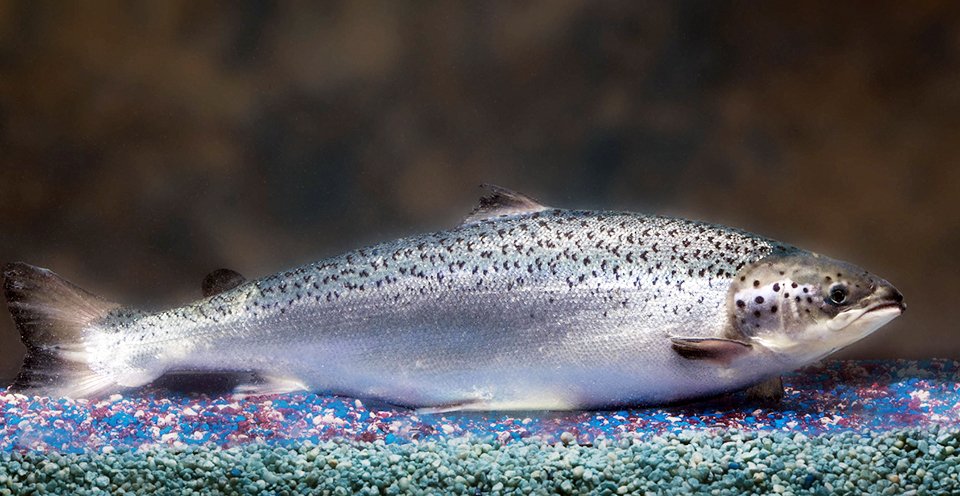
Intelligence
A brief look at genetically modified salmon
If approved by FDA, fast-growing genetically modified salmon will provide a safe and nutritious product similar to other farmed Atlantic salmon.
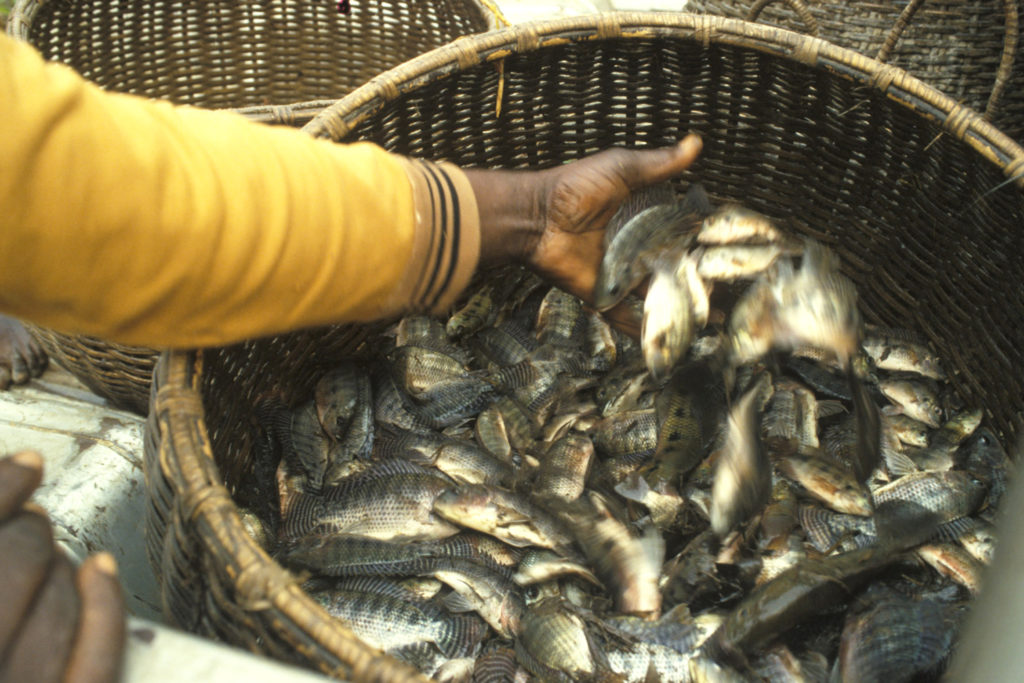
Responsibility
A helping hand to lend: UK aquaculture seeks to broaden its horizons
Aquaculture is an essential contributor to the world food security challenge, and every stakeholder has a role to play in the sector’s evolution, delegates were told at the recent Aquaculture’s Global Outlook: Embracing Internationality seminar in Edinburgh, Scotland.
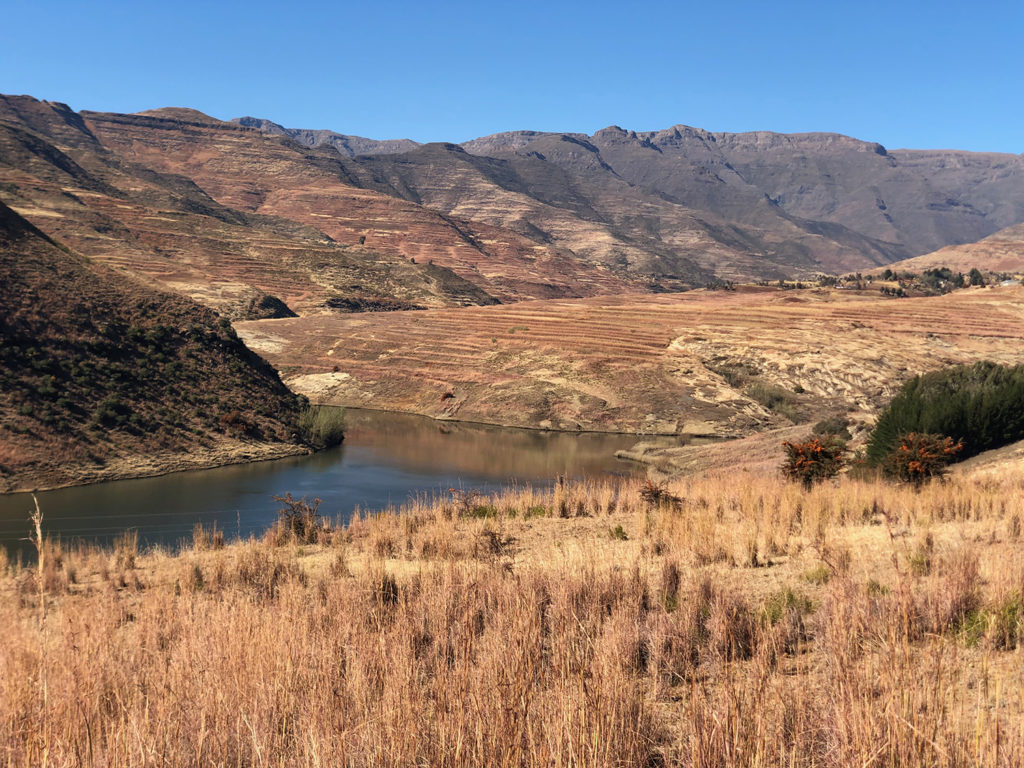
Innovation & Investment
Africa’s first land-based salmon farm a landmark for Lesotho
A Singapore-based company aims to make Lesotho, a nation of 2 million people, known for a local fish that’s truly anything but local: Atlantic salmon.