Alabama-based BioSynsortia aims to make aquaculture and agriculture waste management a profitable endeavor
Microalgae, nutritional building blocks for fish and shellfish, are of growing importance to aquaculture feed manufacturers. Rich with long-chain omega-3 fatty acids, microalgae hold a small but growing share of the alternative-ingredient market.
While the major elements in microalgae production are provided by nature, mainly sunlight, a great deal of space is required to cultivate it. Microalgae is traditionally grown in shallow split ponds that are about nine or 12 inches deep. But the algal cells that are not at the very surface of the water don’t get much light. The ponds are, as a result, large and spread out, making collection costly, inefficient.
A new business formed by researchers at Auburn University in Alabama, USA, is taking aim at the expenses and the very dimensions of this process, first by allowing sunlight to do its job more effectively and without acres and acres of room.
Enter the Circulating Coculture Biofilm Photobioreactor, or CCBP. BioSynsortia CEO Matthew Hilliard told the Advocate to think of the CCBP as a pond-meets-conveyor belt system tailor-made for aquaculture producers like catfish or shrimp farmers who could feasibly use the system to upcycle their waste streams into a useful and nutritious food source. The coculture system comprises both a microalgae and a specific heterotrophic bacteria, a methanotroph that consumes methane, an abundant carbon source in aquaculture effluent.
“Nutrients to grow microalgae – nitrogen and phosphorous – can come at severe costs. Large scale – even lab scale – the cost can be high if it’s in a soluble salt form,” Hilliard said. “Biomass productivity in ponds is low. They need a lot of sunlight to grow. Even if you’re in the desert, with plenty of land and sun, the biggest challenge is then harvesting that biomass.”
Hilliard and his business partners – Dr. Peter He, president, and Dr. Jin Wang, chief technology officer – are colleagues at Auburn, which boasts one of the leading aquaculture programs in the United States, drawing students from all over the world. Auburn works extensively with the U.S. catfish industry, which could provide a business match for BioSynsortia.
Aquaculture pond discharge water is rich in ammonia and nitrites, and for it to be recycled back into culture water, biofilters are required. But by feeding the waste materials to the microalgae – along with another bacteria to consume the carbon dioxide and methane – it consumes the nitrogen and phosphorous in the liquid phase, allowing the microalgae to grow. It breaks down the waste, removing ammonia, and produces a harvestable and edible biomass.
“We envision that our technology will significantly reduce the need for split-pond systems and instead enable farmers to utilize the additional ponds for cultivating more aquaculture products,” said Hilliard.
Beyond the ponds
It’s not just fish farmers who could uptake the technology and create a new revenue stream, Hilliard explained. Dairy farmers would also likely be interested in using the CCBP platform to reduce the environmental impact of the manure generated by their farms.
Mark Stoermann is chief operating officer at Illinois-based Newtrient, which offers dairy farmers across the United States a catalog of waste treatment technologies to manage waste streams, which will soon include other solutions like feed additives. The majority of dairy producers are indeed sustainability-minded, he said, pointing to farmers who produce fertilizer concentrates or those who have invested in renewable energy creation. He said BioSynsortia’s idea could convince some to think even further outside of traditional channels.
“How [dairy farmers] manage their manure in the future could be the difference in whether they stay in business or not,” he told the Advocate. “Can we find a way to address environmental issues to be more sustainable, to be good producers of milk and meat and other revenue streams that future generations can continue to farm the way we do? Will there still be cows? We believe there will be, but without [strong] commitments we’ll be driven farther away from the table.”
While many dairy farmers still look at waste management as a “back end of barn” concern and might hesitate to invest in this area, they know the importance of soil health and the importance of lowering greenhouse gas emissions. Valorizing waste would allow dairy the opportunity to take larger steps toward sustainable production, retain positive consumer sentiment and grow profits.
“We need [additional] revenue streams,” said Stoermann. “For most, the only thing that pays is the milk check. We have to somehow use technologies less costly than new plants at every stream to get rid of phosphorous. Right now, we can’t pay for that because it’s not part of the milk price.”
3D rendering
Hilliard and the BioSynsortia team have a prototype CCBP to co-culture microalgae and bacteria on a belt that constantly moves, providing more exposure to sunlight.
“The cells aren’t blocking each other,” said Hilliard. “In raceways, shadows are cast on the bottom cells. In our configuration, we’re moving those cells that need that gaseous carbon in the headspace.”
“The surface area on the belt is significantly more than the surface area of the liquid surface. It’s three-dimensional, whereas ponds are two-dimensional,” said Dr. Wang. Additionally, cultivation of the cells as a biofilm makes the microalgae cells “more robust and resistant to stress factors,” she added.
A biofilm eventually grows on the substratum of the conveyor belt, which Hilliard said is beneficial for harvesting. Centrifugation and drying processes that traditional microalgae cultivation systems employ “drive costs up, hindering the microalgae industry,” he added.
The goal is to produce a biomass for aquafeed that’s cheaper than terrestrial crops. At present, BioSynsortia is in the earliest phases of its development, but Hilliard said preliminary analysis of biomass composition indicate sufficient protein and lipid content; however, his team is still working on a full composition analysis of the biomass to determine key attributes like specific amino acids and fatty acids.
Follow the Advocate on Twitter @GAA_Advocate
Now that you've reached the end of the article ...
… please consider supporting GSA’s mission to advance responsible seafood practices through education, advocacy and third-party assurances. The Advocate aims to document the evolution of responsible seafood practices and share the expansive knowledge of our vast network of contributors.
By becoming a Global Seafood Alliance member, you’re ensuring that all of the pre-competitive work we do through member benefits, resources and events can continue. Individual membership costs just $50 a year.
Not a GSA member? Join us.
Author
-
James Wright
Editorial Manager
Global Aquaculture Alliance
Portsmouth, NH, USA[103,114,111,46,101,99,110,97,105,108,108,97,101,114,117,116,108,117,99,97,117,113,97,64,116,104,103,105,114,119,46,115,101,109,97,106]
Tagged With
Related Posts
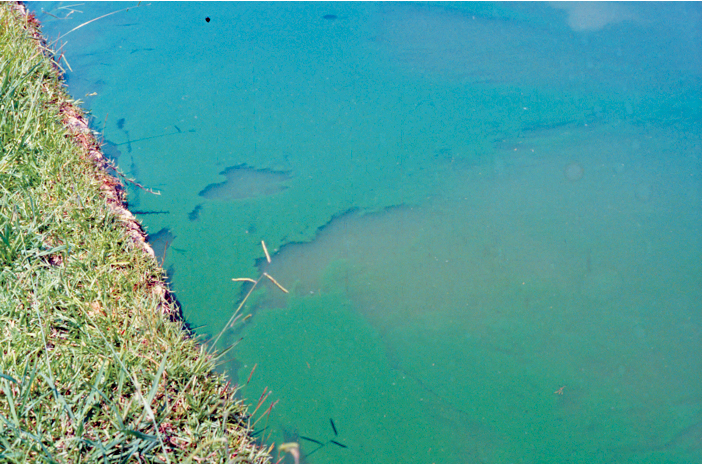
Responsibility
Phytoplankton in aquaculture ponds
Aquaculture ponds typically have ideal conditions for the growth of various species of phytoplankton. Green algae are considered most desirable in freshwater ponds.
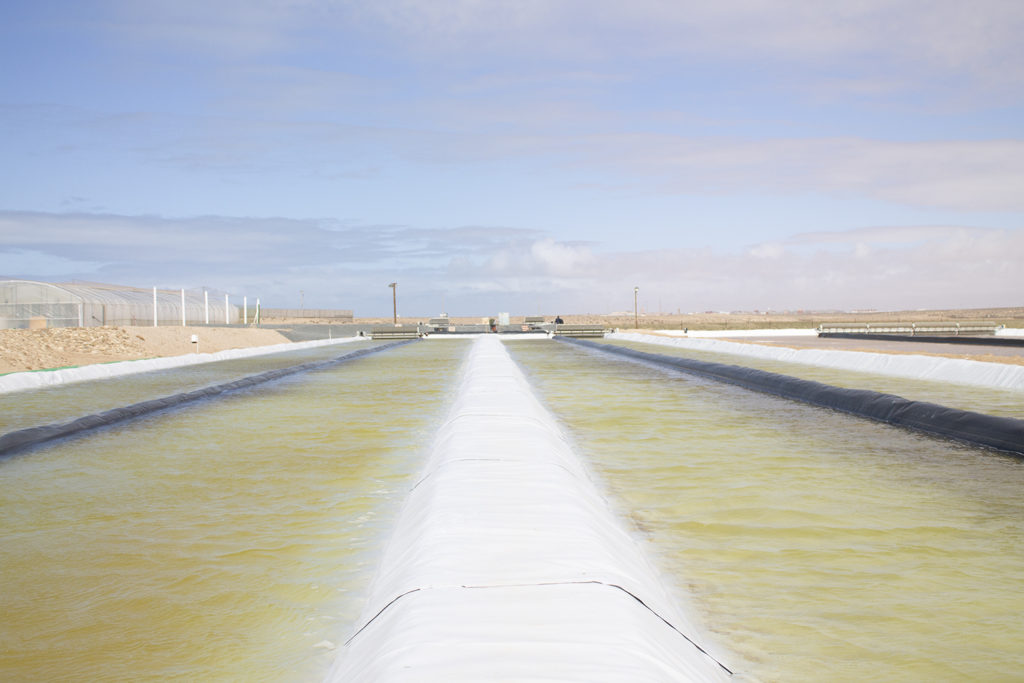
Aquafeeds
Sunlight, seawater and wind: A simple recipe for ambitious algae grower Susewi
Utilizing proven large-scale pond engineering, Susewi aims to become the world’s largest producer of algal biomass, with its sights set on aquafeeds.
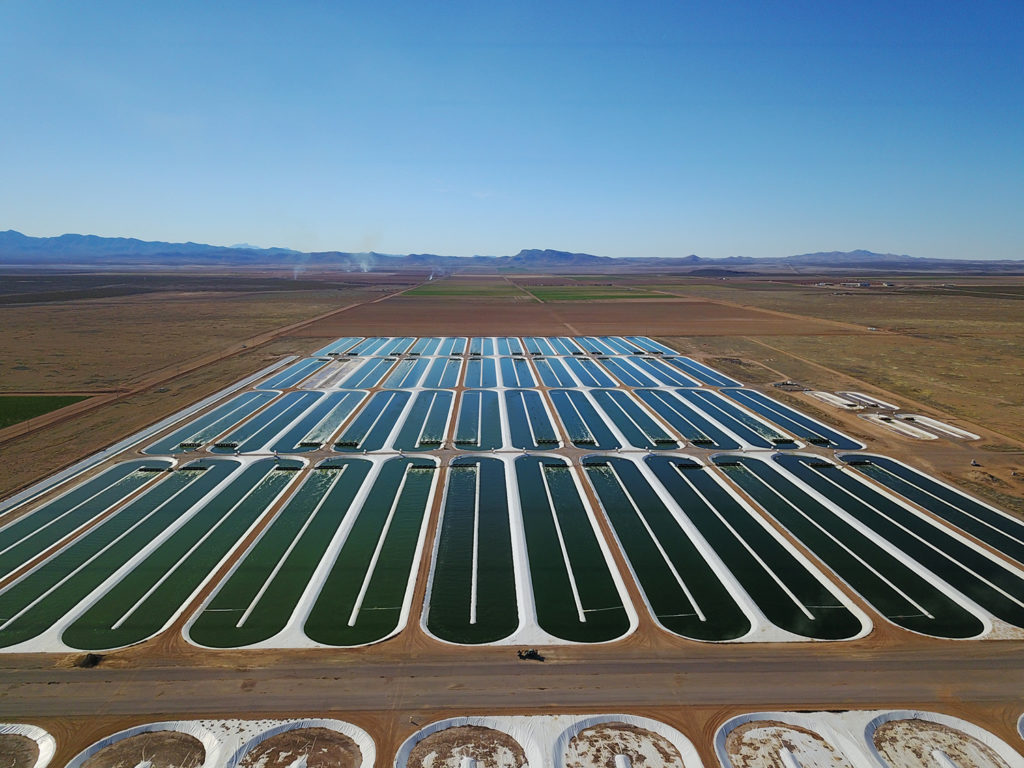
Aquafeeds
Pond-cultivated algae: Slimy superhero for aquafeeds?
Qualitas Health, which grows algae in ponds in New Mexico and Texas for human supplements, is entering the alternative aquafeed ingredient market.

Aquafeeds
Aquaculture Exchange: Rick Barrows
After 14 years with the USDA’s Agricultural Research Service, Rick Barrows talks about the importance of finding ‘complete’ and commercially viable alternative sources of omega-3 fatty acids and continuing innovation in the aquafeed sector.