Ocean on Land Technology’s Algae In-a-Box is a modular, moveable system that works in varied environments, allowing simultaneous growth of multiple algal species
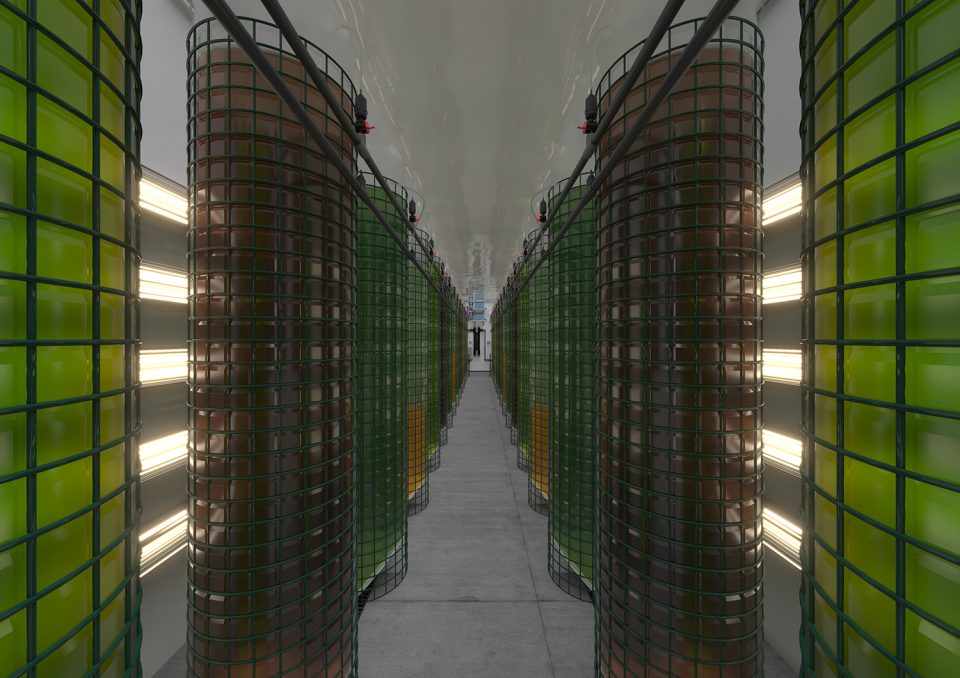
Aquaculture is one of the leading solutions to feed a growing global population with a low environmental impact. Using microalgae – phytoplankton typically found in freshwater and marine water systems – to produce high-quality shellfish is one of the ways that aquaculture capitalizes on resources and technologies that are both simple and complex.
Algae In-a-Box is the latest innovative product from Ocean on Land Technology, a leader in hatchery equipment solutions. Housing an entire algae production lab in a container, Ocean on Land aims to make aquaculture an accessible and viable solution for everyone. Dr. Matthew Johnston, director of research and development at Ocean on Land Technology, details the benefits and the work behind this product.
What was the rationale for creating the product? What problem is it trying to solve?
Algae-in-a-Box is the only true end-to-end turnkey microalgae production system on the market. It not only provides a solution for the laboratory requirements and scaling microalgae stock cultures, but the system also comes complete with a microalgae bag production system, with all the air and water filtration systems required for consistent production. The real cherry is that both the laboratory and the micro-algae bag production system come pre-installed in specially fitted 20 or 40-foot sea containers, with food-grade floors and walls and temperature control. Open the container doors, connect the water and electricity and you are ready for production. It could not be simpler! If you ever want to increase production or move to a new site, well that just could not be easier with the modular sea container concept that is provided by Ocean on Land Technology.
How long did it take to develop it, and what were some of the challenges and wins?
The concept of moving the bag system into a modular container design took roughly six months. The biggest challenge was creating a unique base design for the bag to be supported on. It took four design changes and testing to ensure that the base could support over 500 kg of vertical weight. This was big win for us and it allowed us to move forward with the product.
What are the key differences to other products? How does it solve the pinpointed problem?
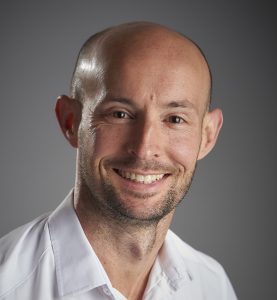
The key difference to the bag system offered by Ocean on Land Technology to other systems on the market is that within this sector we are seeing more and more photobioreactor units being produced. Photobioreactors are fantastic products that enable high concentrations of microalgae to be produced for not only aquaculture but other markets such as pharmaceuticals in a small footprint. Photobioreactors have their place in the market, however, they can only grow one species at a time and have a high initial capital cost. A 40ft algae in a box system with thirty, 350L bags at maximum production has the capacity to produce 7-9×10-12 algae cells per day at a 25% continuous harvest with an average cell density of 3.5 million algal cells per bag. This algal cell output places the algae in a box product in line with some photobioreactors on the market where those operators are striving for consistent and reliable micro-algae output and not pushing their production. The difference being less initial capital outlay and the key capability to produce a range of algal species and cell sizes for your shellfish hatchery produce to thrive.
The bag system offered by Ocean on Land Technology is not a new concept. However, making the system modular and placing it within a “box” and combining this with a laboratory for scaling starter cultures is unique. The bag system enables a range of microalgae species to be produced simultaneously, which for aquaculture and primarily shellfish hatcheries is required to provide a balanced nutritional regime to all stages of production from broodstock condition to larvae and seed production.
The “box” component also means that additional culture rooms do not have to be built onto existing facilities, avoiding project delays and cost uncertainty. In many cases building approval is not required for temporary structures, such as containers, so algae can be grown right away.
What does this new innovative product mean for the industry?
It provides the aquaculture industry with a turnkey solution for their micro-algae requirements. Currently, there is no product similar to this, which is plug and play, modular and easily expandable and movable. Perfect for remote sites which hatcheries often are. It also suits sub-Arctic and tropical, desert locations due to the thermal insulation that is fitted within the containers.
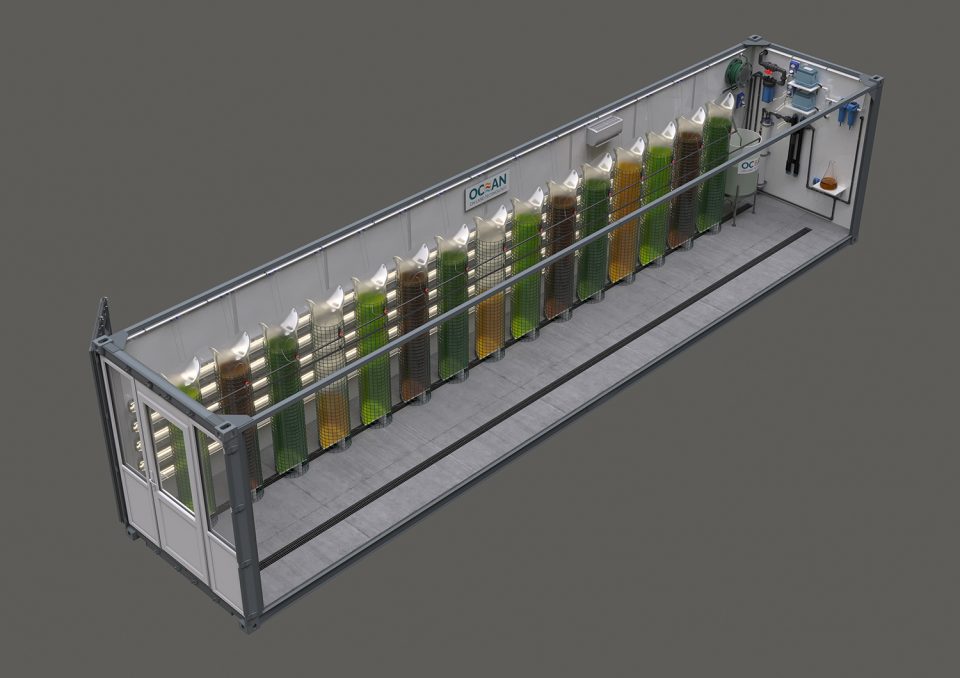
Orkney Shellfish Hatchery case study
After all the hard work was done it was time to put our product to the test in the real world. Orkney Shellfish Hatchery was the perfect candidate as they were just starting off. Situated in the remote Orkney Islands in Scotland, they represented our exact target market.
What problem was Orkney Shellfish Hatchery facing?
Orkney Shellfish Hatchery produces disease free native oyster spat for the restoration and farming markets in the United Kingdom and Europe. Initially investing in photobioreactors to provide two key microalgae species for their production requirements. However, a range of various species is required with most shellfish hatcheries cultivating five to seven microalgae species. To produce all these within photobioreactors for a start-up company was cost-prohibitive, so an alternative solution was required that enabled the company to produce a range of microalgae species.
To be able to provide a range of microalgae cell sizes and varied nutritional profiles a bag system was recognized as the most cost-effective solution to provide this, supplementing the core algal species with a range of species produced from the bag system.
Algae-in-a-box is a truly innovative product designed for a sustainable future. It opens up previously inaccessible markets and provides a commercially viable solution to the demands of a growing population. We hope the work we do at Ocean on Land Technology encourages more people to join, support and give aquaculture serious consideration when thinking of solutions. We believe the blue food economy is a core component of a sustainable future. – Dr. Nik Sachlikidis, managing director at Ocean on Land Technology
How did Algae-in-a-box provide the solution?
The bag system has been around for decades. You typically see this in some form in most shellfish hatcheries. Why? Because it’s cost-effective. Also, if a culture fails to take or becomes contaminated, it’s quick and simple to get a new culture established with little downtime in your hatchery production, and most of the processes are automated in continuous culture bag systems. For all these reasons as well as providing a suite of species with varied cell sizes and nutritional profiles this was the right mix for that hatchery to balance its microalgae requirements for its production.
What are the results?
Today the hatchery has grown its bag system from 12 to 30 bags and has added a further photobioreactor. In essence, Algae In-a-Box made scaling easy as Orkney Shellfish Hatchery increased its microalgae production to meet the growing demand for native flat oysters for the restoration and farming market. Increasing the bag system has provided the hatchery with a range of core microalgae species at a reduced cost point, enabling the hatchery to move quickly to meet its customers’ requirements. They also saved a lot of time as they did not need planning permission to set up a new container. This was what our product was designed to do, and we are happy to see organic results.
Author
-
Ocean on Land Technology